Every year, Alfred Kärcher SE & Co. KG sends more than three million delivery note items from its central warehouse (Global Parts Center) in Obersontheim (Germany) all over the world. This is the hub of the huge accessories and spare parts business of the world's leading provider of cleaning solutions for the private and commercial sectors. In view of growing order volumes, the processes in the storage and picking of spare parts and accessories had to be adapted in order to be able to act more efficiently, quickly and CO2-neutrally in future. Kärcher therefore decided to build a third high-bay warehouse including a new storage pre-zone. This triples the existing storage capacity of around 70,000 items and eliminates the need for transport between the central and external warehouses in favor of a safe, fast flow of goods and higher parts availability in order picking.
The project, which began in 2022, comprised the construction of a new six-aisle double-deep high-bay warehouse with around 32,000 storage locations and the implementation of a warehouse pre-zone including a connection to the pre-zone of the existing high-bay warehouse. Kärcher commissioned PENTANOVA CS GmbH to realize the new warehouse pre-zone with connecting conveyor technology, electrified monorail system circuit, installation of ergonomic picking workstations (goods-to-person) and implementation of new container conveyor technology, including connection to the existing one.
Optimum material flow thanks to electrified monorail system
In order to find the best solution for Kärcher's high-bay warehouse pre-zone, the specialists at PENTANOVA CS GmbH first simulated the expected material flows during the design and project planning phase. On this basis, the decision was made to use the tried-and-tested electrified monorail system (EMS ). It now connects the areas of incoming goods, storage and retrieval, outgoing goods and the picking workstations and ensures optimum material flow organization. Kärcher opted for a 130-metre-long EMS circuit with eight vehicles equipped with chain conveyors to ensure efficient logistics processes in the warehouse pre-zone. Chain conveyors in combination with contour control stations are used as connecting conveyor technology to ensure smooth goods transportation in the storage and retrieval areas.
Thanks to the EMS's frequency-controlled, high-performance vehicles, the system can be adapted to current material flow volumes within a very short time, thus ensuring even workload in order picking. It is also easily scalable. If the shipping volume at Kärcher increases or the warehouse needs to be expanded again, the system can be extended quickly and easily.
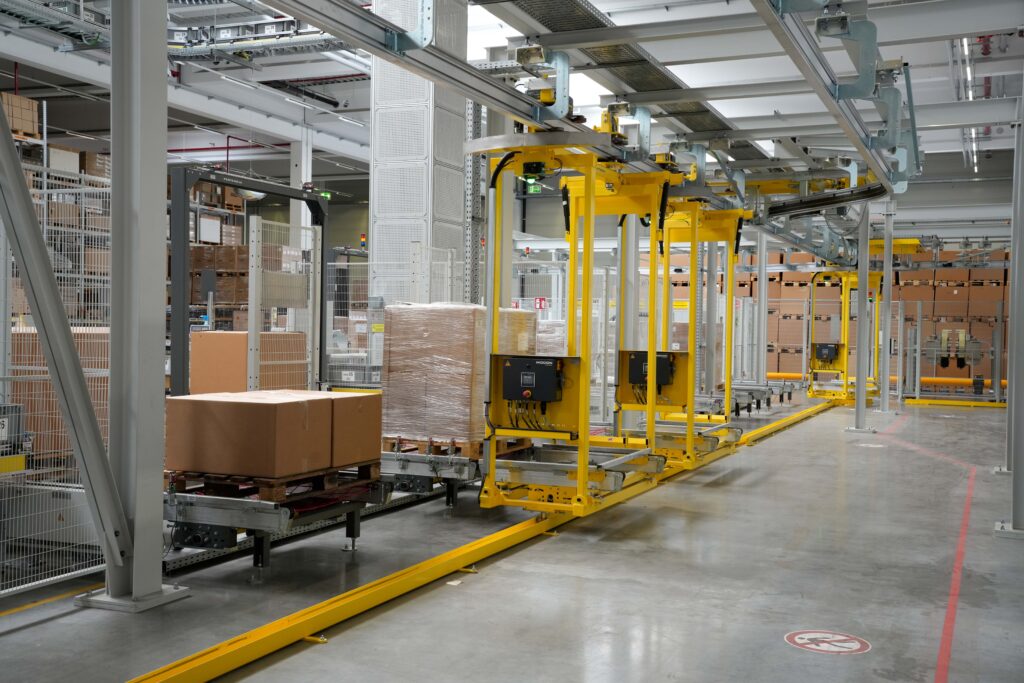
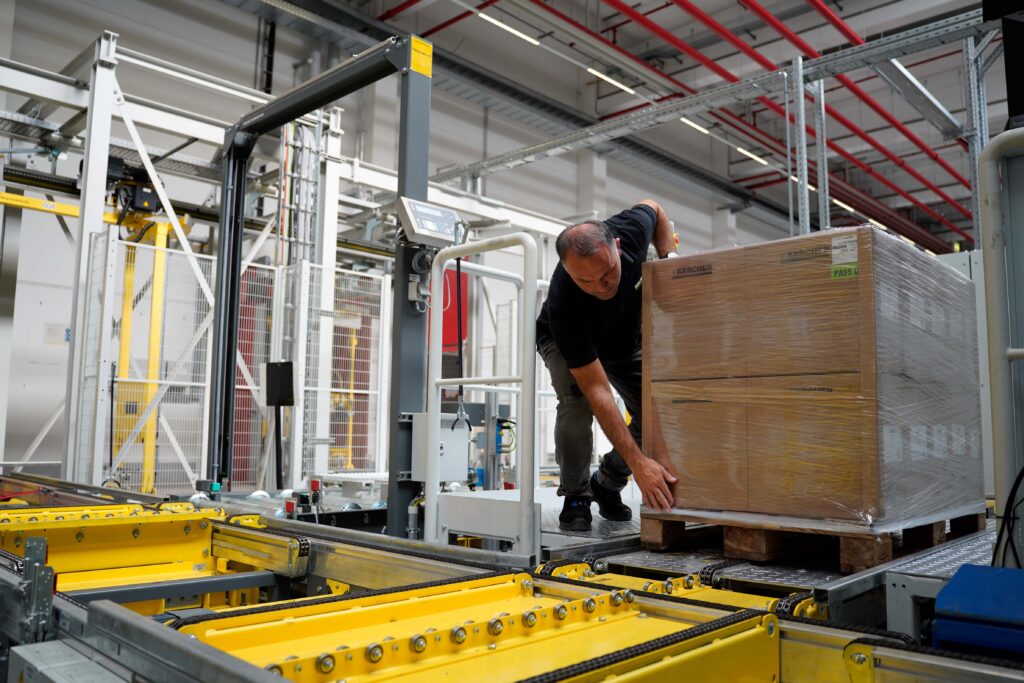
Efficient order picking thanks to ergonomic workstations
The ergonomically designed picking workstations are located between incoming and outgoing goods. The container conveyor technology and its connection to the picking workstations was also part of PENTANOVA CS GmbH's scope of services and is designed for a total throughput of 200 containers per hour. Once the bins have been fully loaded, the order picker sends them on their way to the small parts warehouse. Roller conveyors and a vertical conveyor take the bins to the approximately 200-metre-long conveyor section, which is located on two levels at a height of around five meters and is connected to the existing bin conveyor system.
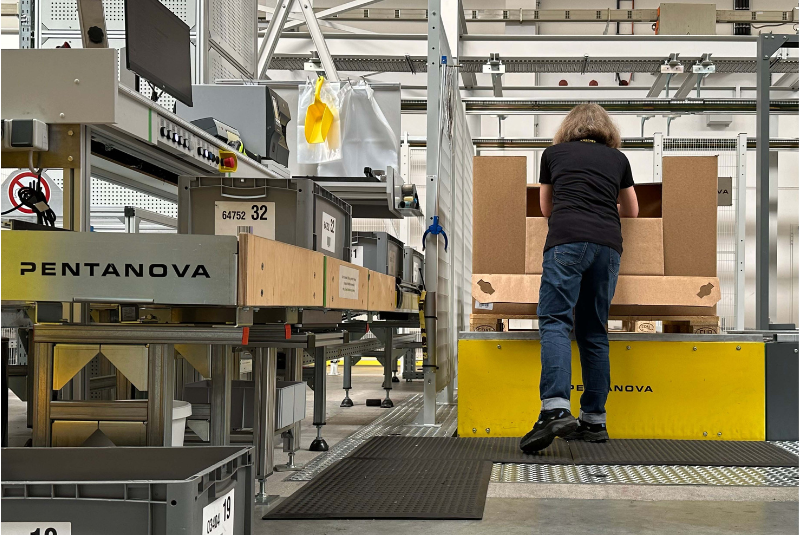
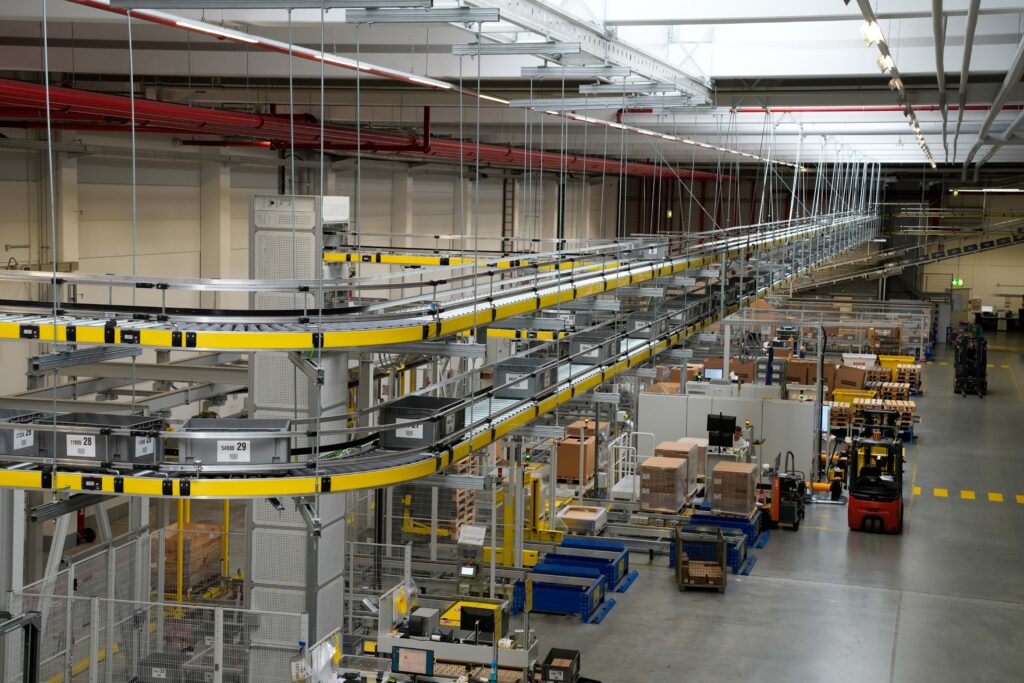
Fast and precise realization
The expansion of the high-bay warehouse and implementation of the new warehouse pre-zone at the Kärcher Global Parts Center in Obersontheim was completed in just 11 months. The customer schedule was met despite all the complications in the global supply chains. The facility was put into operation in December 2022. The adapted processes enable the world's leading provider of cleaning solutions to make its supply chain more efficient, faster, more flexible and more sustainable.